Vector Contour
Vector Contour is a global leader in automatic contour edgebanding in mid-tier to larger manufacturing environments.By automating the edge-banding process in your manufacturing environment, you and your customers will notice a significant improvement in the quality of your products. Operational management is easy and the financial benefits of a Vector Contour system are proven. It’s time to unlock the potential of your business!
The Vector Contour philosophy allows components to be produced in the factory with minimal or no setup. The system is highly flexible, batch size can be 1 or 100+ units. No programming is required which means significant cost savings, better time utilization and enhanced employee satisfaction in a job well done.
Vector Revolution machines use a patented pressure system utilising AI algorithms to automatically analyse the shape of the panel as the head progresses around the panel. It requires no user programming and provides exceptional glue bonds. It’s a game changer.
Our patented technology delivers very high edge pressure to create a strong glue bond and micro glue line thickness. The automated process removes the variability of the operator. Rework is minimised. Consistent high quality output is delivered.
A lower initial purchase investment combined with simplicity of integration into manufacturing environments, high machine utilisation, consistent high-quality output and ease of operator training and management. The financial benefits are quickly obvious to business owners.
Vector Revolution machines are in use in Europe, North America, South America, Australasia and Asia. There are over 80 manufacturing sites using our machines, including businesses in the recreation vehicle/caravan, boat building, commercial furniture, educational furniture and architectural millwork sectors.
We have long standing and enduring client partnerships that are built on mutual respect, open communication and service excellence. Our clients know we will go the extra mile to solve problems and provide the right solutions for them.
Automatic Edgebanding Specialists
Shaped panels are making up a greater proportion of components manufactured in the joinery industry as businesses look to reflect customer preferences. Our customers are differentiating their products for competitive advantage and better financial performance.
Essentially, we make edge-banding easy. In particular, the edge-banding of curved shapes has been regarded as a difficult process in manufacturing environments. The Vector Revolution machines have transformed this thinking and our clients consider their ability to effortlessly edge-band a wide range products, of varying shapes and sizes, an important competitive advantage.
Our Machines
The Vector Revolution Series
The Vector Contour Revolution machines have literally turns contour edge-banding on its head and represents the first significant development of machinery in the composite board industry since the development of CNC machining centres some 20 years ago.
About Us
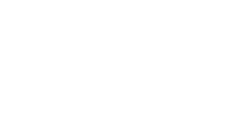
Since 2008, the Revolution Series of machines have been manufactured in New Zealand and marketed globally. Vector Contour now has offices and representation in New Zealand, Australia, USA, UK, Ireland, Germany, Czech Republic, Greece, Norway, Turkey, Japan, Korea and Brazil.
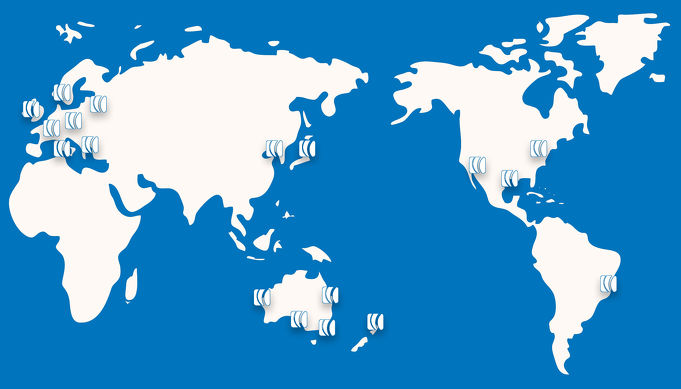